Modern animal husbandry is a very specific business. Its main feature is that it is associated with continuous biological cycles of animals. The price of any mistake here is extremely high.
A balanced and timely proposed diet is one of the main factors affecting the increase in milk production and the increase in livestock, and hence the profitability of the entire production. From the proper management of the feed table, feeding efficiency and animal health directly depend. This is a complex process that complies with stringent regulations. So, cattle are fed 2-3 times a day, depending on the type of feeding and the age of the animals. Distribution of feed by livestock, which is located in one room, cannot last more than 20-30 minutes. The dosage must be strictly observed: the error for stalk feed is allowed within ± 15%, for concentrates ± 5%. Loss of feed that can be collected after distribution can not exceed 1% of their total amount. Irreversible losses are not allowed.
But in practice it is not so simple to strictly follow the standards: the human factor puts the stable distribution of feed into a big question. The diets on the feed table often do not match the recipe compiled by the livestock specialist. It also happens that compiled, prepared and received by animals - these are three completely different diets. The feed delivery schedule is also violated: the person did not have time, he was delayed somewhere, fell ill, there was no one to replace him, etc. This leads to a violation of the biological rhythm in animals and, as a result, to a decrease in their productivity.
The process of preparing and distributing feed accounts for up to 70% of the total labor costs: this is one of the most labor-intensive technological processes in animal husbandry. Is it possible to free a person from routine work, while guaranteeing that animals will be provided with feed exactly according to a given recipe and strictly at a specific time? Yes, if you entrust the feeding process to automation.
Fig. 1. Dairy cattle breeding is a leader in the implementation of robotics
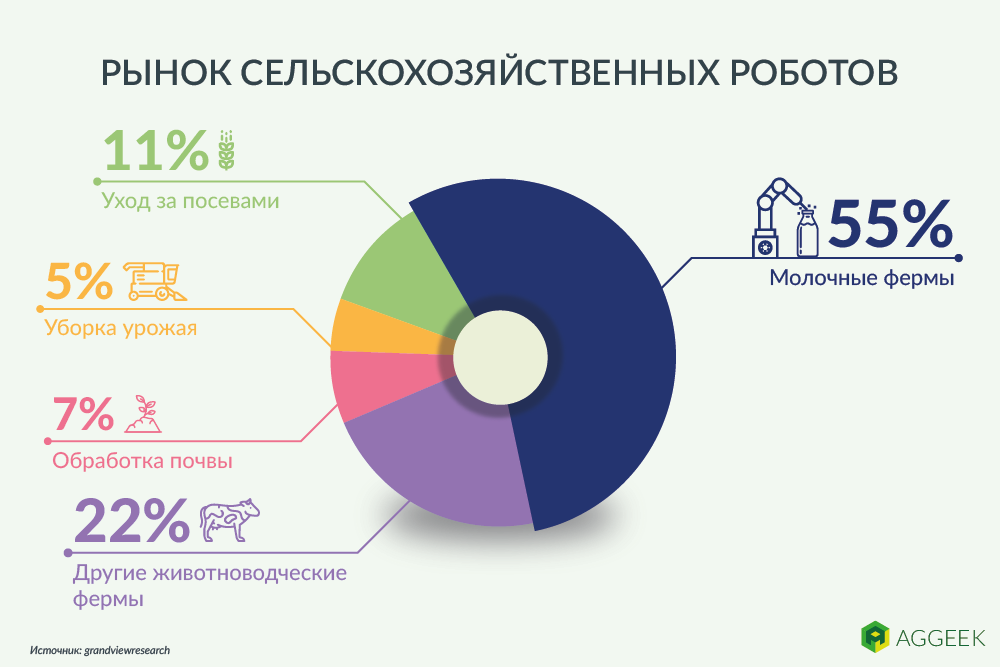
The evolution of the feeding process
Stationary mixers that grind and mix roughage can be considered the first step to automate feeding. Reliable and “working,” they save a ton of time and save you from hard work. Stationary mixers are used mainly in small farms. Distribution of them can occur either manually (the resulting mass is loaded into the tractor trailer and distributed with the help of forks and shovels), or by means of feed-distributing mechanisms.
The next step is the more modern mobile feed mixer. They grind bulky feeds loaded from the silo trench, mix it with concentrate and distribute the resulting mass to the animals themselves. Such mixers can be trailed or self-propelled. They can be used both with a fully mixed and partially mixed diet, and with separate feeding with concentrate. Built-in electronic scales allow mobile feeders to accurately comply with the dosage.
Today, more than 50% of all livestock farms in the Russian Federation use mobile feed mixer. Most enterprises prefer trailed models, which are much cheaper than self-propelled ones: if a trailed feed dispenser costs an average of € 20 thousand, then about € 250 thousand will have to be paid for a self-propelled.
The main achievement of science and technology in the field of optimizing the feeding of farm animals today can be considered the complete automation of feeding, when all processes - selection, weighing, dosing, mixing and feeding of feed - occur without human intervention.
Hanging Feed Wagons
The latest generation of feeding systems includes, for example, suspended feed car systems. The leading positions in their development, production and implementation are occupied by the firms Pellon (Finland), DeLaval (Sweden) and Mullerup (Denmark). In Russia, such equipment was first installed in 2012 at the Dashenka dairy farm in the village of Rotovo, Pskov Region.
The suspended feed wagon moves along the monorail mounted on the ceiling of the barn parallel to the feed table, calculates the components of the feed mixture, doses them and distributes the finished feed in accordance with the instructions of the program. That is, it performs actions similar to the actions of a mobile mixer-feeder, but can do without a person.
The only thing that is required here from a person is to provide storage facilities with forage, from where automation will ship them. And you also need a person in order to program the system: introduce a set of ingredients, composition, norms, dosage, etc. into it. In other words, she needs to once in detail "explain" what is required of her, and then the whole process will be carried out and controlled by herself.
In order to distribute feed in the barn by ground transport - a feed dispenser or a tractor - you need a 5-6 m wide passage. A suspended feed car is enough for 2.5 m. This saves about 15% of the area. Accordingly, the costs are reduced during the construction of the barn. In addition, the use of suspended feed wagons eliminates the ingress of dirt from the wheels of the equipment onto the aft table.
The feed car can be programmed to distribute both roughage and concentrates, as well as their mixture - a fully mixed monocorm. He can distribute food individually to each animal or group of animals. You can even give away the cost of a portion to automation to control feeding within the budget: for this, you just need to drive the price of ingredients into the program in advance.
Fig. 2. Automatic feed distribution system DeLaval

Automatic calf feeding
Automatic calf feeding systems are another example of how, with the help of high technology, the problems of optimizing the feeding of farm animals are solved. Such equipment is produced by a number of manufacturers: including Urban, Delaval, Milkline and many others. The Dutch company Lely is considered one of the pioneers in this area, and the Lely Calm system is recognized as its most advanced development.
The main advantage of such a system is that it is maximally adapted to the natural behavior of the calves and allows them to drink milk at any time throughout the day - as they say, “on demand”. Milk (or its substitute) in the system maintains the optimum temperature for 24 hours a day: it does not cool down, as when drinking manually.
A collar with a transponder is put on each calf. The system monitors how many times it fits the nipple and how much milk it drinks. You can configure the automation so that it gives each animal a certain volume with each approach. A calf that has already consumed its norm will not receive milk. If the animal skips feeding, the system reports this so that the operator can find out what is the matter.
Dirt or insects cannot get into milk: the system rinses automatically. Robot manufacturers also provide another useful feature: for example, the ability to add medicine or vitamins to milk (only for those animals that need it) and the function of disinfecting the nipples after each calf.
But that is not all. The system analyzes the nutritional characteristics of the calf (frequency, portion size, etc.) in order to subsequently adjust to it. That is, the memory of “feed”, as such systems are called, stores all the information about each animal. True, the last word still remains with the person - he has an information display that displays all the data on the work of the “feed”, and with the help of the control keys can at any time make its own corrections to it.
By the way, automation itself also helps to “wean” the calf from it. Upon reaching 2 months of age, she ceases to feed him, giving ordinary water instead of food. Having made several attempts, the calf ceases to approach the nipple, after which it quickly switches to coarse and concentrated feed.
Fig. 3. Urban calf automatic feeding system

Automatic grazing system
Grazing cows in a common pasture often leads to poor feed utilization due to trampling and contamination of faeces. The so-called “frontal” pastures show themselves much more expediently, in which the area with a fresh portion of plant feed for feeding to animals is limited by electric hedges. This, on the one hand, can significantly improve the efficiency of the use of forage resources of the pasture. On the other hand, it significantly increases labor costs, since it is necessary to rearrange the electric fence to a new section of the pasture manually.
In order to minimize the cost of manual labor when grazing in the “frontal” pasture, Lely has developed an automatic grazing system Voyager. These are two mobile robots that are interconnected by a conductive wire, limiting the area for grazing animals.
Robots move at certain distances at predetermined intervals, while each time freeing a new area. The mode of their movement (distance and intervals between movements) is set by the operator and depends on the size of the herd, the size of the “frontal” pasture and the feed ration used.
Fig. 4. Voyager automatic grazing system
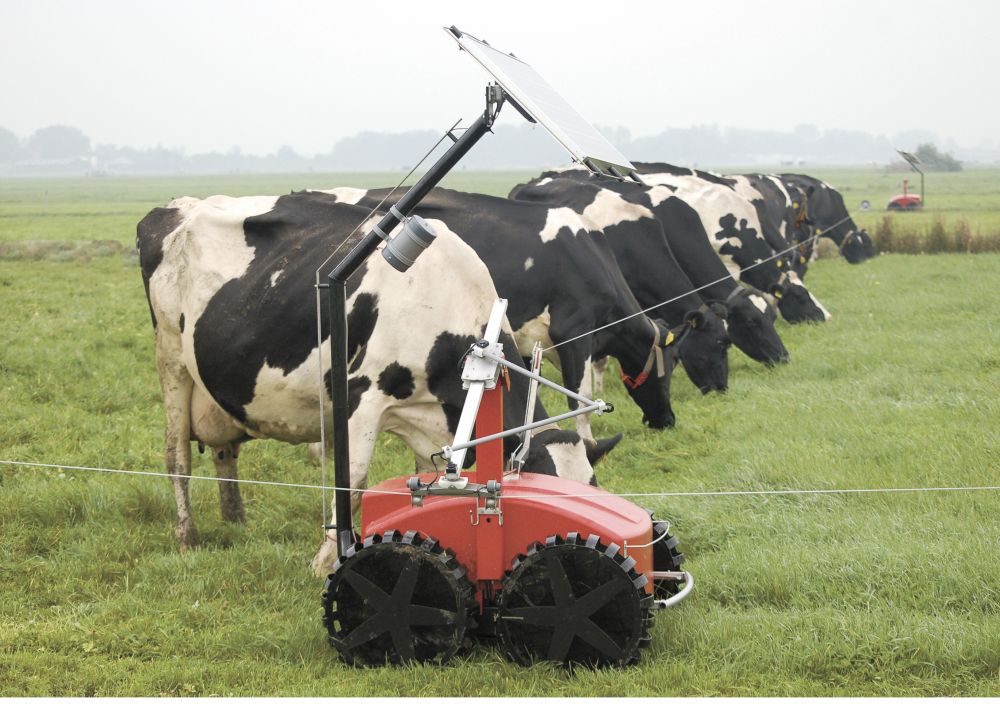
Reverse side of automation
According to experts, the market volume of agricultural robots by 2024 will reach $ 74.1 billion. Their production will grow by almost 20 times: up to 600 thousand units of equipment. It is expected that in the near future a number of innovations in automation of feeding will become available, which are now at the testing stage or at the stage of prototype development.
Fig. 5. The transition of agriculture to robotics will be rapid
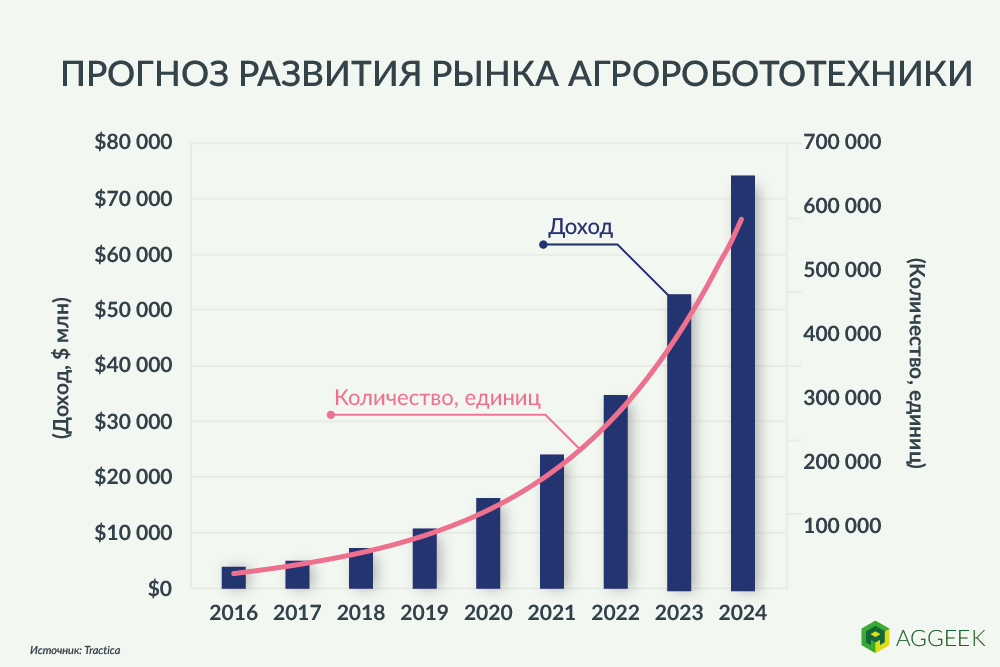
However, like any high-tech solutions, robotic feeding systems have their drawbacks. The most important of them is the high price: for a farm for 200 cows, investments in automation of the feeding process will amount to at least € 450-500 thousand. But you also need forage harvesting equipment, a feed warehouse, silos, access roads and communications.
Automation needs to be monitored by a person who will monitor its work, adjust diets and carry out maintenance on time. Using robotic systems in an economy with poor management is a waste of money. Not a single miracle of technology yields results if there is no competent personnel in the farm that installed it that can manage complex technological processes. Unfortunately, statistics on the lack of qualified specialists for “digital” livestock production looks depressing.
On the one hand, automation requires the acquisition of new skills and staff development. On the other hand, relying on sensors and diagnostic sensors, a person becomes dependent on them, losing independence in decision making. This is especially true for the younger generation, which trusts technology too much. That is why some breeders, especially those who grew up surrounded by animals, are skeptical of innovation.
Another problem is the need to redevelop old cowsheds for the operation of new automatic systems. Moreover, even after reconstruction, many farms cannot 100% meet modern technological requirements.
Nevertheless, automation can increase the overall economic efficiency of the economy, achieve better results while reducing risks, and make labor in this area more interesting and attractive to humans. It should be understood that technological and business processes raise the requirements for the profession of a livestock breeder to a new level. Along with the obvious benefits, new technologies bring new challenges that have to be answered.